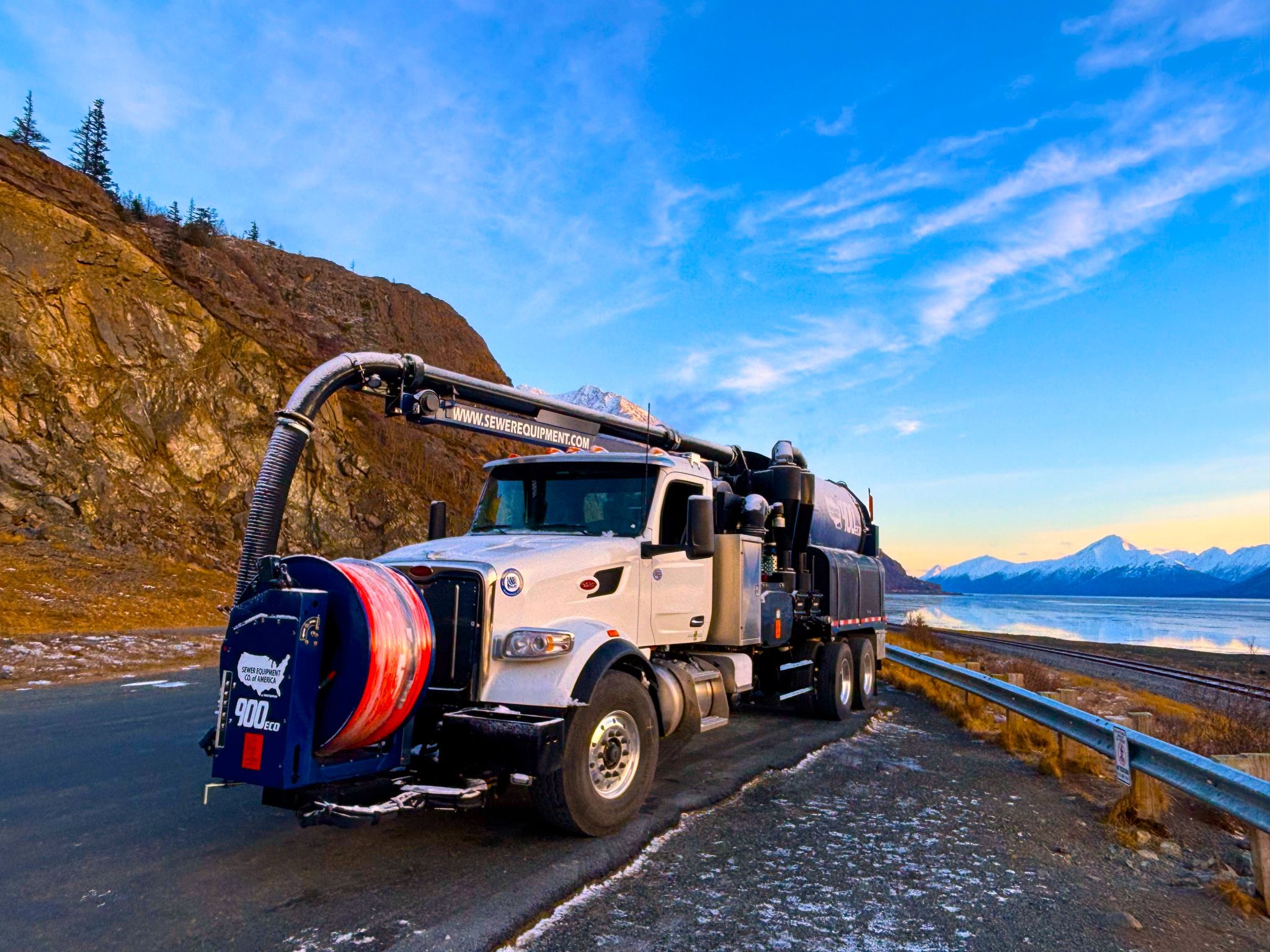
With the price of major equipment in the sewer and water industry nearly doubling in the last decade and projected to continue rising, it’s crucial to maximize every dollar in a municipality’s tight budget. Every truck on the market today offers a range of features designed to do it all, but the effectiveness of these features is a key factor in a truck’s versatility.
A combination truck is already a valuable piece of equipment, designed for high-pressure jetting while also providing powerful vacuuming capabilities. Nearly every truck on the market is equipped with 80-gallon-per-minute pumps and can achieve a minimum of 2000 psi. Additionally, they typically come with an 8-inch vacuum tube and a blower powerful enough for maintenance cleaning at lift stations. Since the capabilities of these trucks are similar, the advantages lie in how each truck is designed to meet these standards.
The three essential factors to consider when evaluating a truck are efficiency, reliability, and ease of operation. When examining the jetting operation, it’s important to understand the type of pump a truck uses—either a Triplex or a single piston. A Triplex pump provides a smoother operation with consistent pressure to the nozzle, compared to the jackhammer effect of a single piston, which experiences spikes and drops in pressure. This consistent pressure helps the nozzle navigate hills and work over joints in the pipe more effectively. It also minimizes streaking in the pipe while cleaning difficult materials like grease. As a result, operators can clean further and more effectively, allowing them to accomplish more tasks in a single workday. Moreover, the smooth operation puts less strain on the reel, reducing jumping and shaking of the hose.
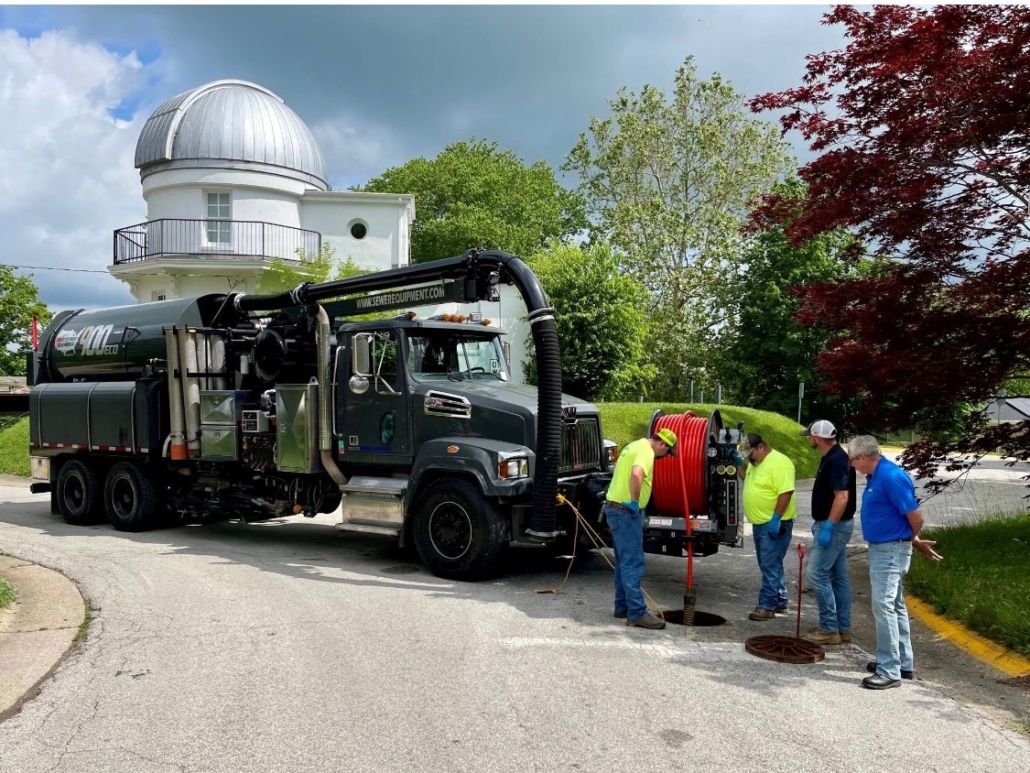
Another reliability factor is the placement of the water pump and the plumbing from the water tanks to the pump. A truck with complex plumbing or a pump mounted above the water tanks can allow air to enter the system, causing the pump to cavitate and greatly diminishing its lifespan. It’s essential that operating the truck is not complicated. Ensuring that on-call operators feel confident in running the truck during emergencies is vital for their safety, as well as for the protection of your equipment and infrastructure. Pay attention to how easy it is for an operator to set up the truck for a job. Observe the location of the controls—having a central area to manage operations can limit unnecessary movement around the truck and streamline the process of running the equipment. The controls should also be simple to understand; a truck that is confusing or requires extensive expertise may limit the number of operators capable of operating it.
Increasingly, combination trucks are being equipped with hydro excavation circuits, allowing them to perform double duty. As previously mentioned, understanding how these features are implemented is critical. The blower is the most important piece of equipment for hydro excavation. Historically, fan units have been the most common type of blower found on vacuum trucks due to their loose tolerances, which allow them to withstand more damage. However, the market is shifting, and more operators are now utilizing positive displacement (PD) blowers. PD blowers, with their tighter tolerances, offer a much higher standard of performance, enabling operators to dig deeper, longer, and more efficiently. The filtration systems for PD blowers have advanced, providing enhanced protection for the equipment. A well-protected blower should have multiple cyclone filters to collect dust, along with a 10-micron final filter to capture fine particles. The larger the cyclone filters and the more final filters available on a truck, the greater its reliability. However, it is also important that the filters are easy to clean, both for operator comfort and to ensure proper maintenance is performed.
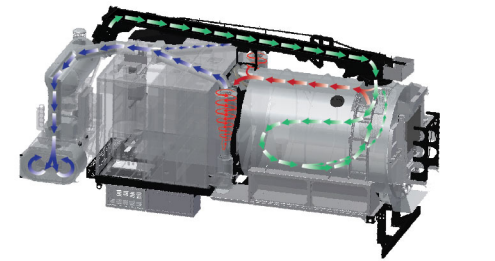
Although most combination trucks on the market can work effectively as hydro excavators, not all of them combine efficiency, reliability, and ease of operation.
When considering a truck, there are additional questions to address, such as wear points like boom tubes or the materials used for the water tanks. These are common failure points on certain trucks that can drain your budget and lead to significant downtime. A combination truck is a complex piece of equipment, but certain aspects should be straightforward. It should be simple to maintain, easy to diagnose problems, and most importantly, straightforward to operate. If your next truck checks these boxes, you are likely to be satisfied with your choice.
If you would like to learn more about finding the best equipment for your needs or have questions about your current equipment, please contact one of our experts. We would love to hear from you!