Model 900 ECO
Combination Sewer Cleaner
MODEL 900 ECO COMBINATION SEWER CLEANER
Sewer Equipment Co. of America introduces the Model 900 ECO Combination Sewer Cleaner truck. The 900 ECO utilizes proven technologies to deliver a machine with a simplicity that is unequaled in the combo jet vac truck industry. As with our leading 747 ECO trailer jet and 800-HPR ECO truck jet, the Model 900 ECO operating platform offers the best in class fuel efficiency and noise reduction for operator safety.
It all starts with our patented “Hydro Drive” powertrain system. The Hydro Drive powers the pump and blower in addition to the auxiliary hydraulic systems. When you are ready to work, simply put the truck in neutral and apply the parking brake and exit the cab while the combo truck remains in neutral and power is taken directly from the chassis engine, assuring operator safety during operation, as there is no transfer case to slip into gear.
Quick Look at Specifications
Debris Capacity: 6 yard, 9 yard, 12 yard, 15 yard
Length: 32‘7" to 41’7" Width: 8‘5" Height: 11’10"
Axle Configurations: Single, Tandem, Tridem, and Tandem w/Pusher Axle
Max Water Capactiy: 600 gallons to 2100 gallons
Max Hose Capacity: 800’ Hose Size: 3/4" - 1"
Boom Extension: 10’
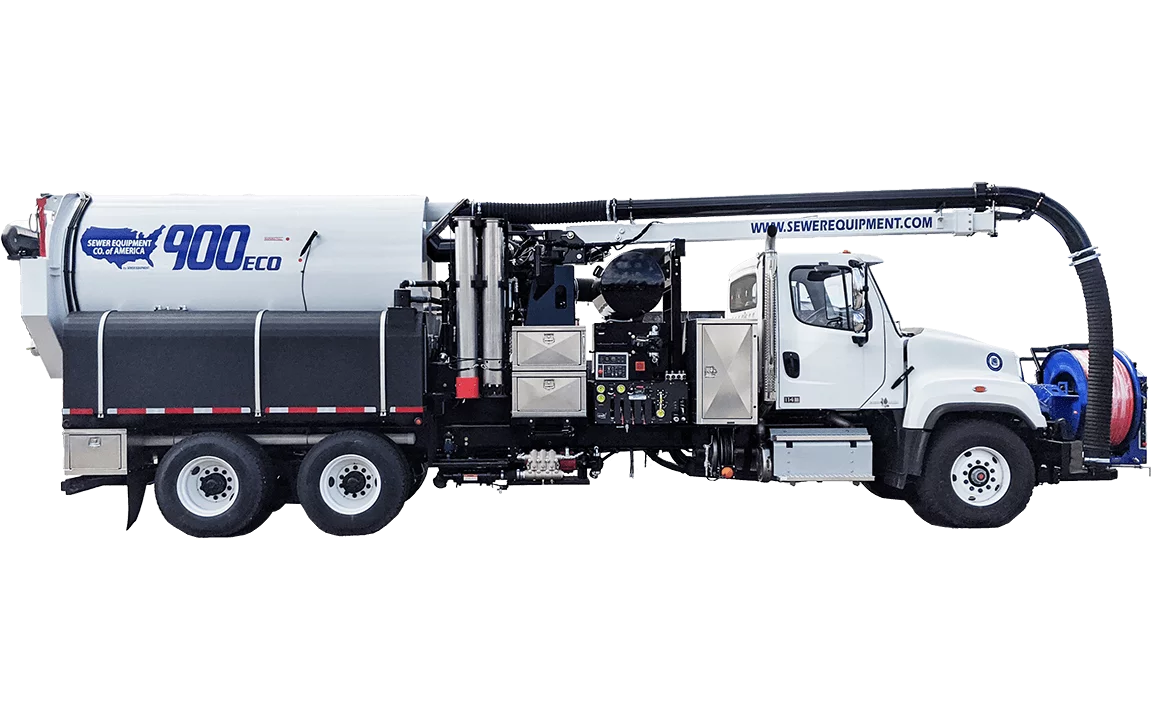
WATER TANK PROFILE: Exclusive Duraprolene® construction offers 100% immunity to corrosion and dents for unparalleled service life and eliminates the need for draining during storage. The fully baffled construction eliminates sloshing and allows safe travel while full, or partially full, of water.
POWERTRAIN: The most advanced powertrain in the industry, our exclusive “Hydro Drive” powertrain system takes all required power directly from the chassis engine. There is no need for an auxiliary engine, and unlike most other designs, our truck remains in neutral while in work mode, increasing operator peace of mind and safety, as no transfer case is needed.
START UP: Operator simplicity begins in the cab. Simply put the truck in neutral and engage the parking brake. That’s it! All other jetting and vacuum functions are controlled from the operator interface on the hose reel.
OPERATOR INTERFACE: Going to work is as simple as 1-2-3-4. Simply engage the following switches:
1. Work Mode – ON
2. Water Pump – ON
3. Blower – ON
4. Throttle – ON
You are now jetting and vacuuming. Compare this to the “rocket ship” controls of other equipment that include touch screens and digital displays. Our easy-to-use and easy-to-understand controls enhance safety and long term reliability, while making an operator’s job more pleasant.
CHASSIS INTEGRATION: Sewer Equipment’s only interface between
our module and the chassis is via the OEM throttle control port. This intentional lack of integration eliminates problems caused by CAN Bus communication issues between the chassis and module, which are typical on competitor’s designs. If this seems like an insignificant detail, please ask for your fleet manager’s opinion.
Simplicty is Key
The simplicity at the operator’s station begins with the flip of one switch: Work Mode. The operator can utilize the remaining three switches (water pump, blower, and throttle) to go to work with ease. What’s more, is that there are no special sequences required, that’s it! Additionally, simplicity continues with the use of 12-volt electrical switches, relays, and solenoids throughout the truck, making it easy for mechanics to run diagnostics and maintain the equipment. Moreover, no special laptops or software programs required; all you need is a simple test light and a hydraulic pressure gauge.
Get the Job Done the First Time
The Model 900 ECO was designed with an intentional lack of integration between the module and the chassis. There is only one integration that exists; the OEM throttle control port. This lack of integration eliminates problems caused by CAN Bus communication issues, typically experienced with competitor designs.
Best Products and Best Local Support
Whether choosing your next combo truck based on altogether productivity, reliability, safety, overall value, ease of operation, ease of maintenance, or any combination of these traits, the choice is simple: the Model 900 ECO.
Air Flow System
The air system is the secret behind our industry-leading performance. Our air system is designed to deliver industry-leading air movement, while providing the maximum protection for your blower.
The first stage in the air system is the debris tank. Air will enter through the boom and material will impact the deflector plate and start to drop into the tank. The air entering the tank, along with the material, is routed from the single 8” entry point to dual 10” exit points located at each side of the entry. Thus slowing down the airflow and improving material separation.
The second stage of the air system takes the air from the tank and routes it into our cyclone separators. At this point, the cyclonic action of these separators propels any remaining material to the side walls and then down into an easily maintained collection box.
In the final stage of the air system, the air moves from the cyclone separators into the dual 10 micron final filters. These washable filters will capture any remaining fine particles still in the air stream before allowing the air to pass through the positive displacement blower.